The history of phenolic resins: the impact of Baekeland and Bakelite
December 18, 2023
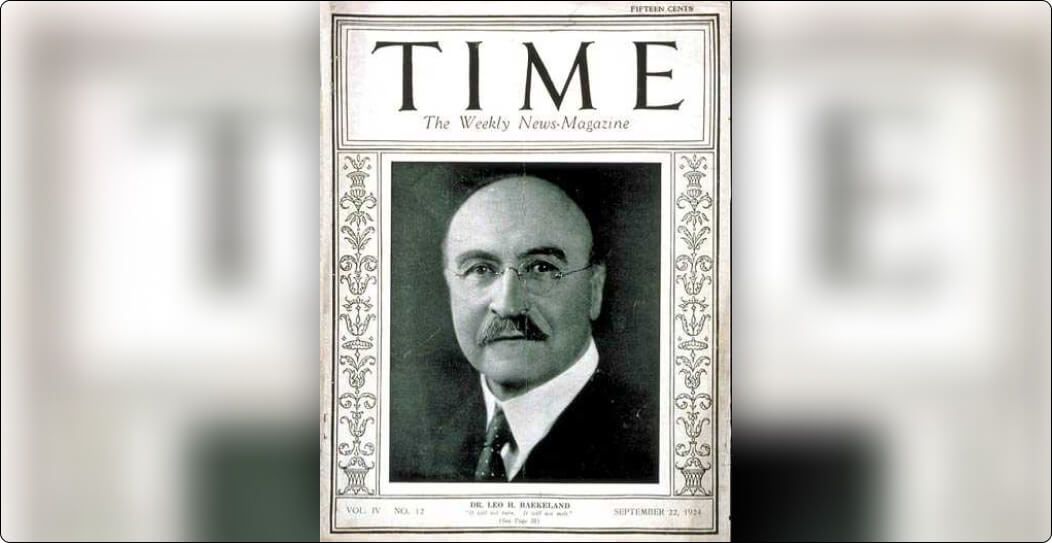
In 1909, the Belgian-American chemist Leo Hendrik Baekeland changed the landscape of the plastics industry forever with his discovery of Bakelite, a revolutionary phenolic resin. Baekeland, often referred to as the "father of the plastics industry", opened the way to new possibilities in the manufacture of polymeric materials.
The genesis of Bakelite
At the turn of the 20th century, Leo Baekeland was looking for a viable substitute for natural rubber to meet the growing demand for insulating and mouldable materials. In 1909, after years of intensive research, he succeeded in synthesising bakelite, the first synthetic resin to harden quickly and retain its shape after curing.
Bakelite resulted from the reaction between phenol and formaldehyde, with an appropriate catalyst.
Bakelite's pioneering applications
Bakelite quickly found its way into many industrial and domestic applications because of its exceptional properties. Its ability to be moulded into complex shapes and its insulating mechanical properties made it the ideal choice for electrical components, such as switches and sockets. It has also been used in the manufacture of kitchen utensils, jewellery and even automotive parts.
Bakelite contributed to the revolution in mass production by providing a versatile and affordable material, paving the way for the creation of mass-produced products, such as the famous black dial telephone.
Current challenges of phenolic chemistry
Although bakelite opened the door to the era of synthetic polymers, its legacy is not without its challenges. One of the main contemporary challenges lies in the toxic compounds used in the synthesis of phenolic resins. Formaldehyde, a key element in the manufacture of these resins, is recognised today for its harmful effects on human health (CMR class 1B).
Today, the phenolic resins industry is at a crucial crossroads. Technological advances and growing environmental awareness have paved the way for new approaches to polymer synthesis. Researchers are exploring more environmentally friendly production methods, reducing emissions of toxic compounds while preserving the properties of phenolic resins.
ResiCare and the future of phenolic resins
The path traced by Leo Baekeland more than a century ago continues to inspire research and innovation in the field of polymers, particularly within the ResiCare research teams! As part of the Michelin group, ResiCare is developing pioneering adhesive resins based on phenolic chemistry. Although they maintain the fascinating mechanical properties of Bakelite, some aspects of ResiCare resins have nothing to do with this historic chemistry. The innovation in ResiCare products lies in the use of non-toxic* compounds in their synthesis, replacing formaldehyde and phenol.
These new formulations also aim to incorporate biosourced raw materials (= from renewable sources on a human scale) in order to limit the use of petroleum resources. And this is one of the objectives of the BioImpulse project!
*Not meeting the SVHC (Substances of Very High Concern) criteria as defined by the REACH regulation.
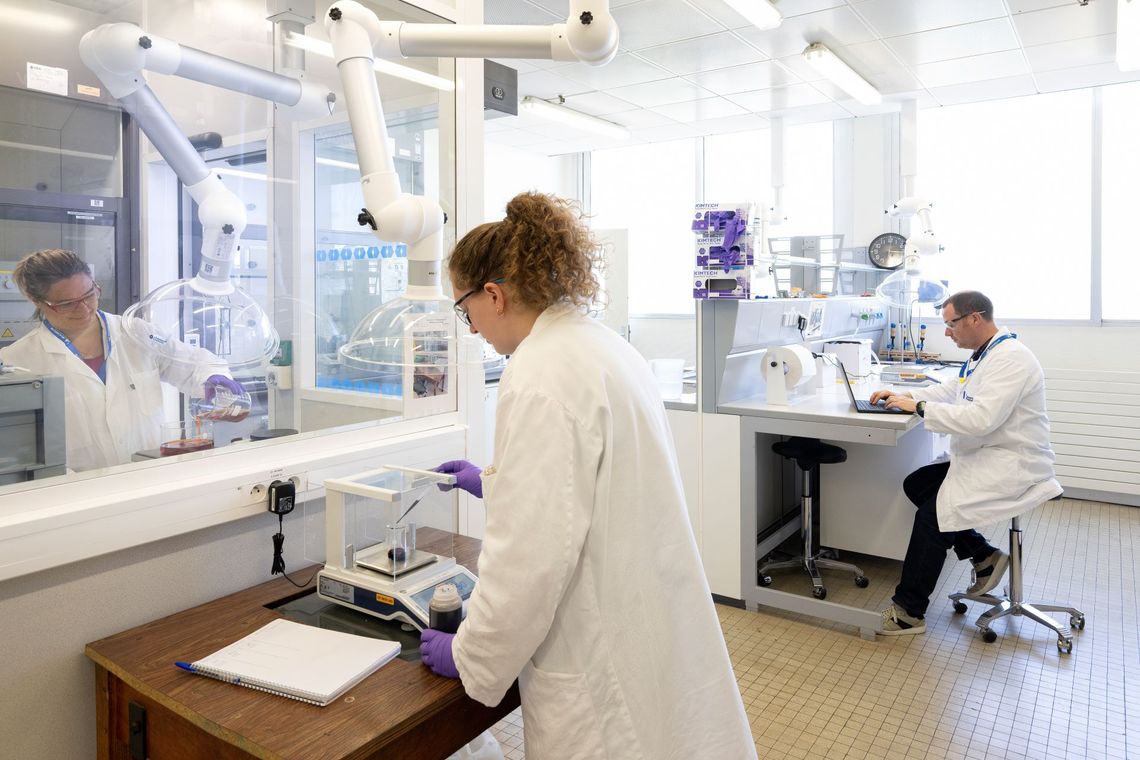